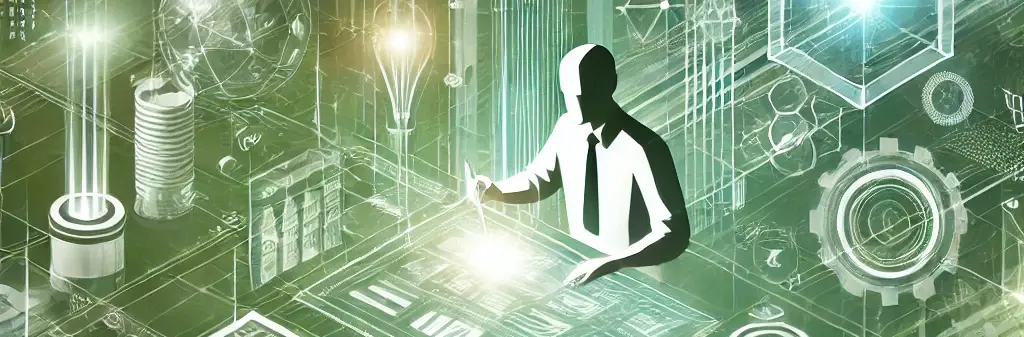
BrightLight Services - Test and Tag
Why Choose Our Test and Tag Service?
-
Qualified Technicians – Certified, experienced professionals who guarantee thorough testing.
-
Fast and Efficient – We minimize downtime with quick, accurate testing and tagging
-
Comprehensive Reports – Detailed documentation of all equipment tested for your records
-
Ongoing Compliance – We remind you when it’s time for your next test to ensure ongoing safety.
Benefits of Our Service:
-
Protect Your Team and Equipment
-
Ensure Compliance with WHS Regulations
-
Reduce the Risk of Electrical Failures
-
Boost Workplace Safety and Confidence
BrightLight Services - AI for Small Business Solutions
Benefits of Our AI for Small Business Solutions:
-
Increased Efficiency and Automation
Automates repetitive tasks, allowing small business owners and employees to focus on higher-value activities. -
Enhanced Customer Experience
Enables personalized and responsive customer interactions, leading to higher satisfaction and loyalty. -
Cost Savings
Reduce operational costs by streamlining processes and minimizing human errors. -
Improved Decision-Making
Provides actionable insights through data analysis, helping businesses make informed decisions. -
Better Marketing and Sales Strategies
Optimize marketing efforts by targeting the right audience with the right message.
Benefits of Our AI for Small Business Solutions:
-
Enhanced Cybersecurity
Strengthens data protection and prevents cyber threats by detecting anomalies. -
Streamlined Operations
Optimizes supply chain management, HR processes, and other internal workflows.Improved Product or Service Quality -
Enhances the quality of products and services by leveraging precision and advanced analytics.
-
Personalization
Enables highly personalized experiences for customers, improving engagement and conversion rates. -
Reduced Time to Market
Accelerates product development cycles and reduces the time to launch new offerings.
Frequently Asked Questions
What is test and tag? Electrical "Test and Tag" in Australia is a safety procedure required by Work Health and Safety (WHS) standards to ensure that electrical appliances are safe to use in the workplace. The process involves testing electrical equipment for potential faults and tagging it with a label to confirm it has been checked and meets safety standards. Australian Standards Compliance: AS/NZS 3760 is the main standard in Australia for test and tag procedures. It provides guidelines on how to inspect, test, and maintain electrical equipment to ensure safety. The standard outlines specific testing procedures and intervals based on the type of equipment, its use, and the environment. For example, equipment used on construction sites requires more frequent testing due to higher risk. The tag includes information such as the test date, tester ID, and next test due date, helping maintain compliance with AS/NZS 3760.Testing for construction, demolition, and mining is conducted in compliance with the AS/NZS 3012 Standard. Work Health and Safety (WHS) Requirements: WHS legislation in Australia mandates that workplaces must minimize risks associated with electrical hazards. Regular test and tag procedures help organizations meet their WHS obligations. Testing ensures that electrical equipment, especially portable and hand-held items, is regularly inspected, reducing the risk of accidents, injury, and damage. WHS regulations often require documented evidence of compliance, including records of test dates, tester qualifications, and any faults identified or resolved. Test and tag is essential for managing electrical safety, protecting workers, and ensuring legal compliance. It’s particularly critical in high-risk environments like construction, manufacturing, and healthcare, where equipment faults can lead to serious incidents.
What is the test and tag law in Victoria? In Victoria, Australia, test and tag laws require employers to ensure that electrical equipment in workplaces is safe to use and regularly tested and maintained. This requirement falls under the Occupational Health and Safety Act 2004 (OHS Act) and is supported by the Occupational Health and Safety Regulations 2017. Here’s how the laws apply: Duty of Care: Under the OHS Act, Victorian employers have a duty of care to provide a safe work environment. This includes ensuring that all electrical equipment and appliances are safe to use and regularly inspected. Employers must eliminate electrical risks where possible or minimize them through effective control measures, such as testing and tagging. Specific Testing Requirements: The testing procedure follows the guidelines in AS/NZS 3760: In-service safety inspection and testing of electrical equipment. This standard specifies how to inspect, test, and tag appliances based on the type of equipment and the environment in which it is used. Testing frequency varies by risk level. For example, high-risk environments, such as construction sites, require testing every three months, whereas low-risk environments might only need testing annually. Who Can Test and Tag: Testing must be carried out by a competent person—someone with the necessary training, experience, and qualifications (typically an electrician or someone trained in test and tag procedures). The law requires that testing be documented, with records of each test, including the date, tester identification, and the equipment’s next scheduled test date. Construction and Demolition Work: For construction and demolition sites in Victoria, testing and tagging portable electrical equipment and RCDs (residual current devices) every three months is mandatory. The equipment used in these environments faces higher risks of damage, so frequent testing helps prevent electrical hazards. Record-Keeping and Compliance: Employers are required to keep test and tag records as evidence of compliance with the OHS Act. These records may include test results, tag information, and a log of any repairs or issues. Penalties: Failure to comply with these safety obligations can lead to fines and penalties, as well as increased liability in the event of an accident.
What is test and tag for? "Test and tag" is primarily for ensuring electrical safety by regularly inspecting electrical appliances and equipment for any potential faults or hazards. This process helps to: Prevent Electrical Accidents: Testing identifies issues like insulation breakdown, earth continuity faults, and leakage, which could lead to electric shocks, short circuits, or fires. Maintain Compliance with Safety Standards: Many workplaces are legally required to comply with safety standards and regulations, such as those from Occupational Health and Safety (OHS) or Work Health and Safety (WHS) agencies, which often mandate regular test and tag procedures. Identify Faulty Equipment: Regular testing allows workplaces to identify and remove damaged or unsafe equipment from service, reducing the risk of injury. Minimize Downtime and Repair Costs: Detecting electrical issues early can prevent equipment breakdowns and the need for costly repairs, while also helping to maintain productivity. Provide Peace of Mind: Tagged equipment gives workers and employers confidence that the equipment they use daily is safe and compliant with safety regulations. This process is especially important in industries where electrical equipment is used frequently or in challenging environments, as these increase the likelihood of wear and tear.
What qualifications do you need to test and tag? To perform "test and tag" on electrical equipment in Australia, a person must be considered a competent person according to the requirements outlined in AS/NZS 3760: In-service safety inspection and testing of electrical equipment. Here’s a breakdown of the qualifications and training needed: Competency and Training: A competent person is defined as someone with the appropriate skills, training, and knowledge to perform the testing safely and accurately. This does not necessarily require an electrical license, but training is essential. Many Registered Training Organisations (RTOs) offer test and tag training courses. These typically cover electrical safety, how to use test equipment, fault identification, and tagging requirements. Completing one of these courses provides the necessary competency for most workplaces. Electrician Qualifications (Optional but beneficial): In some cases, particularly in high-risk environments or where advanced testing is required, employers may prefer or require a licensed electrician to perform test and tag. Electricians have the expertise to handle complex equipment and perform repairs if faults are detected, adding an extra layer of safety. WorkSafe or Employer Requirements: Certain workplaces or employers may have additional requirements for who can perform test and tag, often influenced by Work Health and Safety (WHS) policies and specific industry regulations. Some employers may mandate that test and tag personnel complete refresher training periodically, especially if they’re in high-risk sectors. Record-Keeping Skills: Test and tag procedures require accurate record-keeping, so training usually includes instruction on how to log results, identify equipment, and track inspection dates. These records are essential for compliance with WHS standards. After completing a recognized test and tag training course, individuals receive a certificate of competency. This certification demonstrates that they can safely and correctly test and tag electrical equipment in compliance with AS/NZS 3760 standards.